马上注册,结交更多好友,享用更多功能,让你轻松玩转磨削论坛
您需要 登录 才可以下载或查看,没有账号?注册会员
×
1 引言
应用高速切削(HSC)技术加工制造模具,具有切削效率高、可以明显缩短机动加工时间,加工精度高、表面质量好因此可以大大缩短机械后加工如磨削、人工后加工和取样检验辅助工时等许多优点。国外制造某种汽车车门拉伸模具时,粗铣后应用高速铣削技术比传统铣削工艺增加一道半精铣工序约10h,但精铣时间从36h缩短到30h,并完全节省了其后的钳工平整走刀痕迹工作20h,钳工铲刮从30h减少到4h,钳工抛光从20h减少为10h,总工时从106h缩短到了54h。
生产实践表明,通过引进和应用高速铣削加工技术,尤其是相关的五轴联动铣削、计算机辅助设计(CAD)/计算机辅助制造(CAM)和计算机数控(CNC)技术,有力推动了汽车模具制造的发展。
2 五轴联动铣削
铣削加工能够获得良好的曲线型近似表面。使用球头刀具进行三轴联动铣削时,通过x、y、z3根轴方向的直线进给运动,可以保证刀具切到工件上任意坐标点,但刀具轴线的方向不可改变。刀具轴线上的点实际切削速度为零,刀具中央的容屑空间也很小。如果这些点参与切削,不利的切削条件会导致加工表面质量下降,刀刃磨损加剧,加工时间延长,使高品位的刀具材料得不到充分利用。
与三轴联动铣削比较,五轴联动铣削具有一系列优点。此时,通过2根旋转轴的运动,可以随时调整刀具轴线的方向,使铣刀轴线与工件表面夹角和实际切削速度保持不变。可以更为灵活地设定走刀路径,以满足对工件表面给定的峰谷深度的要求。其中使用球头刀具加工时,无论刀具相对工件处于什么方位,总是在半球面上分离切屑。因此每次总是切下几何形状和尺寸相同的切屑。发生改变的是分离切屑时刀刃的运动轨迹,以及由此而确定的刀刃接触条件和切削几何运动条件。也就是说,可以通过有目的地改变和确定刀具的方位,来影响切削过程和几何运动参数,并可从刀具磨损、表面质量和加工过程稳定性等方面入手优化二者,如右图所示。 9 k, D% D8 B% h5 T# _0 y+ Z$ W) `
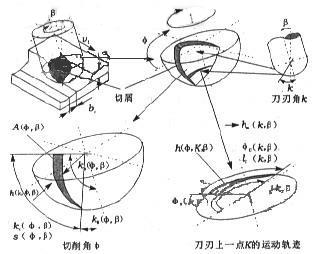 & l: @: D, x5 P. B+ h
球头铣刀五轴铣削几何运动关系图 7 Y7 ? v/ @' v" H) y
当然,五轴联动铣削的数控编程比较复杂,对计算机数控(CNC)系统的计算能力和速度要求更高,在需要机床各直线进给轴作大幅度补偿运动的同时又要求避免发生干涉碰撞。因此在模具制造中,只能利用五轴联动铣削的优点加工一定范围内的工件。
五轴联动铣削可以令人满意地用于加工下凹较浅的零件,例如一种商用车车顶衬里的压铸模。当数学描述复杂的工件表面可以采用铣刀侧铣时,也能够应用五轴铣削加工。国外一家汽车制造配套厂家,利用五轴铣削的走刀行程同时加工出活动组合模具的外形轮廓和压边圈。但是,下凹深且局部形状复杂的模具一般不能够采用通常的五轴铣削加工,因为刀具可能会与工件发生干涉。
限于技术发展当前的水平,五轴联动切削机床2根旋转轴的运动速度和加速度较低,导致五轴联动铣削往往不能够充分发挥高速切削机床的性能和威力。此时,比较恰当的折中方案是3+2轴加工,既保证工件轮廓上各点切削时几何运动条件基本相同,又使轨迹运动速度和加速度比较高。实际运用中首先将工件轮廓划分为不同区域,在各区域内尽可能最优地调整刀具的方位。随后采用三轴联动插补方式切削加工工件各区域轮廓,虽然不能保证切削条件完全不变,但可以避免发生不利的情况例如刀具头部中央参与切削。
实践经验表明,使用圆柱立铣刀五轴联动铣削时走刀间距宽阔,对于所需要的人工后加工反而产生不良作用,因为工件轮廓上指明后加工位置的凸峰彼此间隔也远得多,人工打磨后形成起伏不平表面的可能性增大,这在汽车覆盖件模具是不允许的。相比之下,使用球头刀具走刀间距小得多,产生的近似轮廓上很接近的凹槽低谷,能够为人工打磨模具表面指明方位。
模具工业对机床工业提出了特殊要求,其中一个突出的发展趋势是五轴联动机床。统计数字显示,德国一些专门化机床生产厂家全部产品的50%~80%提供给模具制造厂家,其中有至少16%最多达到50%~60%的五轴联动控制机床。甚至还有厂家批量生产和提供最多可以六轴插补的数控机床,主要用于加工斜面和孔。除此之外,仍然有相当比例的仿型铣床提供给模具制造厂家,不过数量逐年下降。通用机床生产厂家也有很高比例的产品提供给模具制造厂家,但主要用于加工制造中小模具,如家用器具模具或玩具模具。其中五轴联动机床的比例不高,仅占大约3%~5%。
机床的每一根运动轴都是一个误差来源。五轴联动机床上2根旋转轴运动的出现,使得加工精度比三轴联动机床较难达到指定数值,但0.1mm数量级的模具制造精度不难达到。机床制造厂家认为,精度问题不是决定性的,并没有阻挡投资生产五轴联动机床这一发展趋势。影响五轴联动机床运动精度和速度的首要因素是控制系统的性能,然后是驱动系统的性能,以及机械设计的水平。
3 模具加工的自动控制
只有建立从产品设计、工艺规划、数控编程到铣削加工的全局观念,也即CAD/CAM技术集成一体,才能够为五轴联动铣削自由表面提供适宜的实现途径。 拥有五轴联动机床的模具制造厂家,对单单只采用CAM技术的做法提出了批评。在实践中可以发现,汽车制造配套厂家有一小部分工作,是直接利用CAD数据经由数控铣削完成。而大部分的工件几何数据,还是由客户以仿型样件或设计模型的形式提供。不几年前,汽车工业开始要求完全放弃使用样件和模型来制造模具,尽管这一目标短时间内不容易实现。
与仿型铣削平均加工精度为0.6mm相比,数控铣削加工精度较高,可以控制在0.2mm以内。淘汰仿型加工和模具涂色配刮,还可以防止产生累积误差。例如单是温度的变化,就能够在大的样件上造成大于0.1mm的尺寸变动。再如当成品模型或其零件损坏后不可修复需要更换时,对连接表面的加工精度要求在5μm之内,只能通过直接数控铣削获得。实际经验表明,这样生成的表面,需要的人工后加工工作量可以减少50%。这些实在的优点,对于模具制造具有决定性意义。因此,越来越多厂家完全直接应用数字控制技术,来制造全部模具。
经过努力开发,象三轴联动数控一样,在现代模具制造中五轴联动NC系统也允许操作者通过控制台旋钮让机床超速进给,以便尽可能提高刀具的移动速度。面对用户的抱怨,即经由CAD数据、CAM处理器、NC处理器和后处理器正常生成NC加工程序时,后继编辑和补偿所需的数据在机床控制系统中已经不复存在,控制系统制造厂家正在改变方法,把全部CAD数据直接传送到CNC系统中提供利用。这样一来,尽管NC加工程序中并未包含例如同切削点法向矢量有关的信息数据,NC系统仍然能够进行三维的刀具补偿。此外,还允许直接在机床旁方便地改变例如加工策略、刀路、使用的刀具、工件位置等工艺内容。仅仅这一项技术改进,可以成倍提高数控加工整个过程的运行速度。
针对NC编程语言影响过程运行的速度和精度的问题,有制造厂家把改进目标放到要让NC系统能够较为直接地处理曲面的CAD描述上,也即不经过NC编程语言中间搭桥。其结果,使NC系统处理程序块的正常时间降低到2ms,最短时间可达到0.5ms。这样一来,NC系统的速度不再是瓶颈,需要拖带沉重工件即汽车模具的进给驱动系统转而变为薄弱环节。
由于CAD数据经常存在缺陷或不完整,还有NC系统制造厂家便想方设法方便用户介入CAM过程,去发现和修正不正确的数据,但刀具补偿还是由NC系统完成。此时除了补偿刀具长度,还可以在狭小的公差范围内补偿小的、重磨的刀具的半径,并且不需要改编刀路。以上这些制造厂家目前提供的NC系统,都可以对五轴联动铣削加工补偿刀具长度和工件位置。
另外,对模具制造具有重要意义的速度预控制(前瞻)功能,已经成为现代CNC系统的一个标准特征。这一功能的设立,可以使NC系统预先处理多个即将到来的程序块,以便进给加速度和刀路速度与被铣削的工件轮廓相适应,不让进给速度在每一程序块终结时降低到零。在模具制造中常见的自由表面,往往要求加工时密布中间插值点,这时利用前瞻功能可以控制机床产生平滑的轨迹运动,同时保持很高的刀路速度。有制造厂家进一步开发成功具有适应前瞻功能的NC系统,能够在运行过程中作机床误差补偿。另一方面,由于需要的计算量太大,目前机床控制系统还不能够通过在线计算发现加工干涉情况,需要在今后继续努力改进。
4 结束语
五轴联动高速铣削加工技术在汽车模具制造中应用日益广泛,推动了汽车模具制造的发展。应用五轴铣削加工需要注意到适用的工件形状、有利的加工方案和合适的刀具。只有通过综合运用计算机辅助设计/计算机辅助制造技术,尤其需要努力加强机床计算机数控系统的功能,才能够充分发挥五轴高速铣削加工的优点而取得成效。 ; J* G" y. v0 o6 L: J- c) E* T
|