|
马上注册,结交更多好友,享用更多功能,让你轻松玩转磨削论坛
您需要 登录 才可以下载或查看,没有账号?注册会员
×
由于硬脆材料具有很高的硬度、强度及良好的耐热性、低的导热性和热膨胀性,其应用范围越来越广。世界很多国家非常重视其开发和研究。硬脆材料加工方法的研究是关系到它应用前景的重要课题之一。目前,硬脆材料的加工,基本上都是应用金刚石砂轮在高精度的平面磨床上磨削加工,其生产效率、表面质量等存在一些问题,需要进一步研究新的加工方法。因此,我们提出在精密磨床上安装振动工作台,通过带动工件振动磨削。振动磨削时,在一个周期内,磨粒随时改变切削方向,并多方面地参加切削,形成一种“多刃磨削”过程,使工件表面切痕彼此交织,形成低的表面粗糙度值,而且磨粒由于砂轮或工件附加了振动,实际形成一种脉冲切削,磨粒更易破碎,不断形成新的磨刃,在砂轮工作表面上,有效磨粒和磨粒的有效磨刃数也都显著增加,提高了磨具的切削能力,也提高了磨削质量和效率。
5 b% b/ g( Q# N; O, A P* W8 H' Z" [2 b8 S$ e" p+ z) d) m, a' A; ~/ J- f5 J1 H @
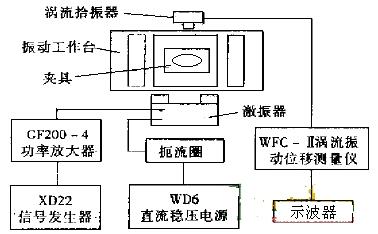 图1 振动磨削试验装置简图 |
2 n0 O! T6 [6 i1 试验装置、条件及方法8 P9 E ^) p' x8 g
铁氧体材料振动磨削是在精密平面磨床上进行的,采用工作台振动方法磨削。工件通过专用夹具固定在工作台上,振动工作台安装在平面磨床电磁吸盘工作台上,可随其纵向移动,振动工作台由振动弹簧钢片支撑,在电磁激振器作用下,带动工件横向振动实现振动磨削。具体试验装置如图1所示。 . V4 A# W! T) B! ]. |0 B5 \/ `
+ g; D; ]0 d% N. g& D
- 试验条件 ) v1 U9 W7 H, W0 B2 o
! V: U/ _8 q5 t) g" O( \2 s- 试验用精密磨床为M170,最小进给量为:0.01mm/ 次:
6 x+ C' j4 d1 i5 x
- 试验用材料为压热烧结Mn-Zn 铁氧体,尺寸为:20×20×20 及Ø18×2数件两种,表面已粗磨,用工作台上的小型专用夹具定位和夹紧: 2 u( r' y) U; ^( U1 x
- 试验用砂轮为40号白刚玉砂轮,采用钢基座金刚石笔修整,砂轮径向跳动量控制在0.01mm 之内:
" h7 |6 p {$ p0 b$ T5 f
- 检测表面粗糙度仪器为英国产Tayor-Hossor轮廓仪(测量精度比真实值小一级)。
: ^+ L* m; I) k1 s- a- | - 实验方法
; Q( C; D- x! g7 S2 R, u( |' W) l
$ c3 j l9 k5 O0 K y! Z4 q4 a- 每磨一个试件样品前,用金刚石笔修整砂轮,修正导程为0.05mm/r,修正深度为0.01mm,修正次数为2 次: / u5 _4 K. s4 h' x
- 工件横向进给量为0.2mm/ min: V: [4 r D6 K$ q
- 磨削深度为0.02mm/次:
( h% R8 c9 B8 k3 C
- 纵向工作台速度为13.0mm/min:
& k/ F2 ?9 T8 \7 @0 f7 m0 {$ Q
- 在每一个固定激振频率和工作台振幅下,向下进给5次,光磨2次: * w4 t) F( S8 X' n
- 磨削液为NaNO3水溶液:
R- I+ A2 h6 V
- 砂轮转速为1500r / min。
" n: G+ \; Q4 X1 \9 d, A1 O7 H% e
2 实验结果& \- K) _+ I& n3 v5 ?1 x8 O
我们先后对数个零件在上述实验条件下进行了磨削,其磨削零件表面经过清洗和干燥,先后在高倍显微镜下观察,然后,用粗糙度轮廓仪检测其表面粗糙度。根据已掌握的资料,在低频振动(20Hz左右)和小振幅值(全峰值为:1mm左右)下,就可达到很好的振动磨削效果,因此,在实验中使振动磨削受迫频率范围小于40Hz,振幅范围小于2mm。为了准确起见,把每个试件测量3次,再取平均值作为试件磨削后的表面粗糙度值。表1为实现恒频率变振幅下振动仪器调整值及其试验结果。表2为实现恒振幅变频率下振动仪器调整值及其试验结果。 ) Q$ ]/ X8 g; w4 p7 Y
9 q/ p2 J$ a5 F( N/ r* }9 D- ^3 ]! S2 b( r* M8 _' L7 f3 j+ p$ M) Q2 M2 u1 A% z! A/ @: N) Y: a3 _; {, q2 L3 Z+ Y0 H- M n- S' l9 t; D# y) g3 ?! G' _7 W$ z- Z$ O1 D/ N5 | }, y9 q# L, p. s; D% v* X# z) [/ j- a( B/ ~$ O# {5 R1 Q( _+ E* X3 m& D0 X" r2 u) \4 h. d$ a4 ?9 r3 ^7 M5 @% X2 F9 Y1 }9 W3 N) Q5 ?, K) ~- ~+ A2 F0 z9 P3 G4 v! Q. t$ U& A' D7 Z+ l( M% M- R' q$ `; P v7 Y: J2 G1 B6 r% U% o N/ o& h$ |5 x6 p |) R' H0 y# ?( n; X$ L% h! S7 q9 c$ `% M2 d3 `8 C$ T0 h4 I7 m( x- u9 w5 K" x+ {, F5 j) q$ P2 A7 g2 x3 n. M9 q$ U- E- f7 W, y& r# P; n/ w' a" r8 x0 S. C4 J5 }( W: O. {2 T& x+ V) ?5 J- ]/ E5 C0 I- C& V S% B* l& Q( [- x; ] w+ @# _7 x& ^' X2 d; R) W4 J, g7 ]7 R/ J- t" G/ ^: d6 K9 E. G% G+ D4 i8 K( G ^3 `6 O/ b" j% J) g# q) t8 l6 H' q& |5 t& t' c; |4 N) X9 ^, M- E) _6 d* V' N8 j4 j- {3 s9 y2 O. Q) @+ M( G3 X$ a( M: H$ @3 _0 U: o& c& D! N2 b& V6 f! T. J4 z/ A/ F; |% F9 h" }7 B- ?4 O3 A% N& ^* Y4 e ~+ l6 l7 _% v7 q/ l! s/ i% b+ \& H$ Y5 l0 m& |9 C% P1 e0 P* G) a, h; r& A, J% W! b5 z' p8 A4 n5 t, H( |; e7 r, a( d4 d/ A4 A; K/ I3 d. D% r- s: _ n% t( Y3 w2 Y4 t5 \2 A- O) B4 S/ f7 z/ r) H. I+ ]0 l) ^$ q) \5 S7 [8 N8 y; i. B5 _' H( B: v' n2 e6 b* V! W; y% ~: X2 p* }- Q# I9 J' Q% n/ H. w, c+ n% A o/ m( q9 \9 M9 P, t- ]" T' p4 O( J5 m& |; L5 e$ R# T( M' m" E! A3 E) L& z! {; N. L& ?# A, i8 _- t( r6 n7 z$ F9 P+ W/ t! G' c# r$ ~8 k4 q0 L& M4 L- \' S! J' f, w' S" `# L# P7 ?$ V, N( o: Y1 W( Y# N7 ]8 |: r( h. ?' }, Z2 J0 o% s W( Y/ i" X P r/ y# L" h# E5 y( i' \7 P' k f$ M d( D. F* W, Q- c0 t* H ?: Q; W8 k4 w* N0 Q; g) g' ~, q3 k, p. a/ Y8 ]1 Z. _. @+ s, N# y4 T; a* G7 h0 ~' `6 A$ ~+ p1 C2 U, o" i: r6 m$ n# m: @4 ?4 s7 F- b+ k( V$ b5 O0 V& u; Q. k# m! q2 h1 r0 w4 Q* [. `! ?; o& |" k: f6 l5 L+ O, R o2 J( C4 |+ G( n! G3 I& a; u/ o$ D h f9 K- k. I6 g; d; m2 x2 b- Z" U" v( T4 J; D" Z' N8 Z$ L, V7 R! L( |, B7 q L9 a4 [& H6 _! G/ I$ T$ E* x% v% U- p \# E' M. O) }3 _! Z, l! g" Q% K) y) b$ P. U! e6 m- e3 @) a% V) O( h; t) ]& a# b. T' T m6 y8 e' U9 @" r! _/ \9 E. x- [% X0 Q7 Y( c1 Q- B7 C) Z- t; t1 Q: A: H( I( G' F, P" Z: a8 y6 \0 k" c- \& G. D4 C, n: K# K6 n4 G" e" ], K# g$ s, s
表1 恒频率变振幅下振动仪器调整值及试验结果
工件编号 |
表面粗糙度测量值(µm) |
振动工作台振幅值 (mm) |
功率放大器 GT200-4型(A-V) |
直流稳压电源WD6型 |
信号发生器XD22型 |
第一次 |
第二次 |
第三次 |
均值 |
电流(A) |
电压(V) |
电压(V) |
频率(Hz) |
1 |
0.23 |
0.14 |
0.17 |
0.180 |
0.6 |
33.0 |
9.0 |
40.0 |
1.15 |
10.0 |
2 |
0.14 |
0.20 |
0.19 |
0.177 |
0.8 |
42.0 |
11.5 |
50.0 |
1.30 |
10.0 |
3 |
0.11 |
0.13 |
0.17 |
0.137 |
1.2 |
47.0 |
14.0 |
60.0 |
1.40 |
10.0 |
4 |
0.10 |
0.12 |
0.16 |
0.127 |
1.4 |
54.0 |
15.0 |
65.0 |
1.70 |
10.0 |
5 |
0.10 |
0.15 |
0.12 |
0.123 |
1.6 |
65.0 |
16.0 |
70.0 |
1.80 |
10.0 |
6 |
0.12 |
0.13 |
0.11 |
0.120 |
1.8 |
69.0 |
20.0 |
90.0 |
1.85 |
10.0 | $ P* A1 Q, f- N$ _
$ Y( u1 p+ \. D1 A7 I% \- G7 u1 d4 V% R1 ]( a$ g) b: [/ D9 M; z4 g& m9 w1 {" k! s/ r4 q: n! L& X& [ ^" h4 `% N! W2 a" B2 g! a. o W! k* _ w' G* T1 } S- u1 W/ S( v0 R7 q: {5 D' b. L# D6 s0 D4 G6 ]$ \& ]* m" a4 x: n; y! `2 m' Q( [% C/ C' T& `9 N5 }% q R2 u# `8 j n8 j# A& l2 [3 p7 g |) `* e0 U# C9 x( P( N* n1 m+ ~7 i5 B" {: s9 V4 C5 l q+ J' b2 `+ [, n& X& u# v7 i+ \* L* A3 z! D& Z3 H( r _2 D8 Q' e0 ?4 Y) I- v( P5 C; Q% b, x! G" U4 F$ {0 [% K& N: M& R; c% ^1 h# P; f% K2 C) f( o4 y5 H4 r1 d$ z0 B0 q8 G/ c( w/ B! i1 ]. ?4 ~/ {& S! w! C( i! M o3 A6 {4 Q! F( I) x. g! ]* }" Z0 D; u/ M* K6 s+ }1 A0 I/ g. b8 q! _; ~( d: m" i5 c7 S6 b4 d; U1 g4 k( o3 O$ F/ {( T" y% X0 _/ n6 r: r: g" h1 }6 ~0 R+ D3 ]) {* p% q J& C3 ^, s: G7 Y7 S* h& F+ i& k. A0 I8 {' {! L6 b- f$ V% ~, i0 [, C: V. S& y3 }0 P! K& u# o( l' Y i$ ?* ?1 d. l7 U; \7 M3 J& l5 [6 D' T- E( J& _) Y$ u' v$ m& K1 J" X t+ Q2 Y' F X+ s3 k' g4 ]. Y. E! O$ i& i$ X4 R& \8 u* t0 `. h4 w) Y+ b: N1 W* c4 G- |: F( c+ X6 D; g9 A1 Y3 J$ b4 G. H# I6 z; j" Z& A8 _3 C; S8 C0 y4 K J0 }% p2 _0 \- S+ O2 ^( [8 P# \3 P( z+ R8 Q/ x" }, J* u8 I6 a) ^5 {% p6 Q( E& |/ d7 `% e4 P. h4 r* @; o2 W+ E+ n2 N& }5 x8 k. a; a2 h3 z4 d2 O6 |1 K+ e. V+ C$ o' J3 t& B$ | b. f9 k6 y; A$ e2 Z( S/ n2 V+ h2 X9 L0 z, v' |1 Z5 F. U5 m8 c" _. F/ B. ?1 R9 Q# f' r7 h) d6 X" i- R8 E T) g- W) @* S6 H) B& |# `" t& ^6 S5 j7 A* Y7 @2 V) Y" ^4 F& u/ H% y( k8 i- h6 c1 }7 Q! T* g+ N. e6 G; U! ? ~0 e. h7 E6 T+ U$ g! |4 R1 Z t! j' d5 v/ l* v8 B' |$ x/ u: I! ]/ X8 V. ]1 W1 u' G/ s# r3 A! N( x+ r7 n* |7 Q, f& G) O5 `) N- X6 Y- h) y. O# T8 J3 c" x) f& d5 ?1 N [. k+ w |* a; ?2 B, v1 w& }$ O4 r+ o% a! a+ x" S: e( i- g3 \0 d: g: V5 d* g+ V5 U3 n& [' j8 C4 A9 V7 b* Y) S+ Z" A) L& J0 D4 z' s0 i" d% ~* R, B& Q( X( i( M2 Y e' t+ Y$ ?% L4 e. w& B$ a! g1 l6 R, C8 c3 [/ _& J9 y G8 j6 V1 N* X8 D( j8 I" M g! a8 h8 D' K+ D4 Y8 H v4 N4 s/ n( s. E4 u! d0 W/ F' J/ `. F) l# m$ a8 Z1 R0 R% H2 D0 y1 t- @! ~3 y1 w, x. |$ E, J0 y6 l( u; E0 E0 w4 f7 I/ p3 }6 N8 x, m1 g% F$ E( J" R: \0 E. T- f r6 Q# G, N7 f6 e0 O: j" Z* N) V3 A8 E( N9 J4 n9 z" x6 A- O5 w) d7 o1 O. v( C, N3 j3 Z& K! e' @ W2 b4 Z5 B2 X1 {, W* Z; e( `3 c* R4 n0 Y; {8 ?6 u5 E! t1 X8 i4 x4 p, o/ x, @5 B. X8 p4 e. l0 H6 _! H) ?$ K" W3 m" T% t" X: m) ^2 E7 v6 R* q7 {. D$ U7 d+ S( C$ `9 t3 C1 r3 ]8 Z6 N& ?1 x; a2 K0 `: K+ r6 ` r+ X+ U) e0 d7 |# Q, D4 N) o! ]8 i+ ]- D3 E1 c* ^, Y# s O7 _+ R6 U8 C `8 }- @/ E `( S/ U. I1 w y+ `; e5 N; w& ~6 n2 g
表2 恒振幅变频率下振动仪器调整值及试验结果
工件编号 |
表面粗糙度测量值(µm) |
振动工作台振幅值 (mm) |
功率放大器 GT200-4型(A-V) |
直流稳压电源WD6型 |
信号发生器XD22型 |
第一次 |
第二次 |
第三次 |
均值 |
电流(A) |
电压(V) |
电压(V) |
频率(Hz) |
7 |
0.22 |
0.14 |
0.18 |
0.180 |
0.8 |
34.0 |
13.0 |
50.0 |
1.30 |
5.0 |
8 |
0.14 |
0.20 |
0.23 |
0.190 |
0.8 |
42.0 |
11.5 |
50.0 |
1.30 |
10.0 |
9 |
0.16 |
0.18 |
0.13 |
0.157 |
0.8 |
37.0 |
11.0 |
50.0 |
1.30 |
15.0 |
10 |
0.10 |
0.15 |
0.18 |
0.143 |
0.8 |
26.0 |
11.0 |
50.0 |
1.30 |
20.0 |
11 |
0.19 |
0.17 |
0.16 |
0.173 |
0.8 |
14.0 |
11.5 |
50.0 |
1.30 |
24.0 |
12 |
0.25 |
0.26 |
0.24 |
0.250 |
0.8 |
15.0 |
11.5 |
50.0 |
1.30 |
28.0 |
13 |
0.13 |
0.14 |
0.13 |
0.133 |
0.8 |
20.0 |
12.0 |
50.0 |
1.30 |
35.0 |
4 n# V" F) A! O# n% Z, C2 a3 实验分析
* T* H2 Y( R( F% D+ g6 n磨削加工后,主要考查了工件以下两种情况。 % v1 g' g! ~/ M. {" {. `
9 S, f/ ~( t/ A; ?
- 工件表面的完整性
. ]+ g1 u) c q" j
- 因为铁氧体材料是硬脆材料,磨削加工后表面的凹坑、裂纹、划痕等表面缺陷情况是标定工件表面质量的重要特征,为此,我们应用金相显微镜分别观察了同等条件下的振动磨削试件和普通磨削试件,发现如下特征:
/ C0 Z% i: s$ r" T% ^' ~
$ L- P# v) o- I/ a5 a- 在普通磨削中,存在明显刀痕。即磨粒在表面划过切痕,切痕槽两侧有一定塑性变形,而在振动磨削中没有发现切痕。 0 K; I4 ~8 l( h0 k1 {1 c$ V
- 尽管振动磨削中切削深度更大,但和普通磨削相比凹坑分布均匀,凹坑的面积大小和深度都明显低于普通磨削的情况。
3 S h' {0 [+ c- y% b6 K - 砂轮是一种多切削刃加工,其圆周表面具有很多位置不同的磨粒,再加上工作台纵向往复运动和振动工作台的横向振动,使得不同位置磨粒在工件表面上所切削的沟痕是相互交错的,因此,形成良好的表面质量,达到加工要求。从硬脆材料切屑形成过程可知,硬脆材料受到磨粒切削时,最初产生微裂纹,而后扩展到使材料成块状脱落的裂纹,裂纹的长度和深度增大,随之出现块状切屑,其大小决定工件表面的凹坑和深度。振动磨削时,由于其特有的方法,在一个周期中,磨粒改变着切削方向,并多方向地参与切削,无数颗不同位置磨粒同时这样做的结果,就是每颗磨粒的切削长度被许多其它磨粒的切削长度截短,形成相互交错网状的切痕,而这样做的结果就是当工件表面的微裂纹刚随着切削的进行迅速发展,尚来不及在长度和深度方面的裂纹相遇,彼此贯通了,也就是在还没来得及发展到普通磨削所达到的断裂程度之前,而提前发生了脆性断裂,自然形成的块状切屑体积就小得多,因此,在工件表面留下的凹坑无论大小和深浅都比普通磨削时要小得多。
0 E0 [2 }: I* J) Y7 f9 O0 P { - 工件的表面粗糙度分析 9 [" o! t7 f0 l1 t8 E% h
- 根据表1中试验结果可以看出,随着振幅的增大,表面粗糙度值在我们考查范围内(<2mm)具有逐步下降的趋势,如图2所示。在磨削加工中,随着工作台振幅的提高,切痕的相互交错截断增强,由于砂轮表面数以万计磨粒彼此相互增强了这种截断交错作用,使得每一个磨粒自身的切痕被截断得更短、更密,因此,被磨削表面微裂纹发展贯通,而脱落的块状切屑变得更小,从而工件表面留下的凹坑面积更浅、更小,即表面粗糙度值下降。根据表2可以绘制出频率和表面粗糙度的关系图,如图3所示。从图中可以看出,它们之间并不具备某种趋势,只是在20Hz左右得到了最好的效果,而在9.8Hz 和27Hz左右振动激烈,出现不稳定状态,效果最差、振动磨削本身是一种受迫振动,当其激振频率和激振对象固有频率相等或接近时发生共振。当工艺系统发生共振时,水平振动不稳定及垂直方向振动加大,导致表面粗糙度恶化。而9.8Hz和27Hz正是共振频率区,因此,振动磨削时,要达到好的效果必须避开共振区附近的振频带,且要提高系统垂直方向刚度。
& v. e4 p9 {/ F6 z l4 O: d0 W [( X, b3 _& y: p; e' x( K) a3 P }! L" ?: W! v; f# F9 H* f* G" m5 y5 m P5 U ~# \& G4 I1 ^7 @- Q9 N* L0 \
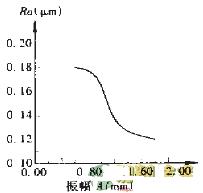 图2 振幅-表面粗糙度之间关系图 |
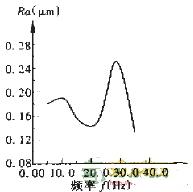 图3 频率-表面粗糙度之间关系图 |
& ~$ C! R; r. `" u/ m4 结论
4 P7 p( G p+ h$ h
5 a+ o* ]0 y1 A8 ]. l- 振动磨削作为一种新型有效方式,具有普通磨削不易达到的良好工艺效果,无论是表面粗糙度值,还是表面缺陷分布等指标都比普通磨削理想: % [4 p* d" D9 O X! |6 p# n) m
- 以垂直于砂轮线速度方向工作台横向振动为特征的振动磨削方式,其切屑形成机理表现为表面微细沟槽成形,可以解释磨削效果与振幅、振频的变化关系:
! q0 m8 l% r& |6 `5 Q
- 振动磨削对机床设备,特别是振动工作台部分的制作和装配提出了较高要求,没有高精度的振动装置就会降低甚至抵消振动磨削带来的优点:
! X/ l9 Z# `0 J9 e( v
- 振动磨削进行时,应该避开工艺系统的固有频率带,一般在低频振动或超声波振动磨削。
( Q2 _$ u; u/ U7 t+ l. @8 C* T; _ |
|