|
马上注册,结交更多好友,享用更多功能,让你轻松玩转磨削论坛
您需要 登录 才可以下载或查看,没有账号?注册会员
×
过去,超硬刀具材料只有金刚石和立方氮化硼两种。人类从使用天然金刚石开始,到20世纪中叶研制出了人造的金刚石和立方氮化硼。人造的超硬材料后来出现了不同的制造方法和类别,而且在不同的工业生产和科技领域中得到了广泛的应用。 % y2 s2 z5 y8 x3 M3 `- v
近年,一种新型超硬刀具材料——氮化碳(CxNy)涂层得到了发展。美国物理学家A.M.Lin和M.L.Cohen用分子工程理论设计出了新型超硬无机化合物氮化碳。根据体弹模量的计算,它可能达到甚至超过金刚石的硬度,从而引起科技界和材料科学家的重视,A.M.Lin于1994年公布了新的研究成果,采用可变晶格模型分子动力学(VCS-MD)从头计算法,扩展了CxNy的理论研究, CxNy可能具有三种结构:六方晶系的b相,立方晶系的闪锌矿结构和三角晶系的类石墨相。A.M.Lin和M.L.Cohen分别计算了CxNy的晶体结构,至少有7种不同空间群结构的CxNy,取得了不同结构和空间群的密度、晶格常数、体弹模量和能量的计算值。它们虽具有相近的能量值,但其他性能的数值差别较大。武汉大学王仁卉也对7种结构的CxNy粉末衍射谱进行过计算。 ' M2 W4 Y# ]2 W
武汉大学物理系能用的反应磁控溅射法在不同的刀具上沉积CxNy薄膜,它是一种超硬材料,具有高硬度、高耐磨、低摩擦和强导热等性质,这些性质和金刚石十分相似。它的化学稳定性也好,可以对铁基材料进行切削加工,故有广阔的应用前景。 0 O' g$ r+ u) H5 p$ N; e5 S
本文主要用武汉大学物理系提供的CxNy涂层高速钢麻花钻和CxNy涂层硬质合金刀片进行了切削试验,探讨了它的切削性能;对CxNy涂层薄膜的机械性能也进行了一定的介绍。
* m; |0 @0 G7 R1 氮化碳薄膜的力学性能
+ [1 Z: [9 p% u, M! H1 x2 Z* C1 \在不同的基体材料上沉积CxNy薄膜,其表面显微硬度测试值列于表1。表1除6号试样为硬质合金基体外,其余1~5号试样的基体均为M2高速钢。 # D4 e2 T7 [0 H. Y
# p9 D4 l' s9 c- O, e5 j, X" l1 V/ I& I, w0 O! j( b1 S( Q/ i8 ]* M! A- k5 f& a: H/ \9 u; z' B; ^% M: I" f) W: |. k) t1 T s g' [5 f K. Z) ?5 J+ V- s/ ~5 T; x7 |6 Y) i0 W$ o1 ~4 a6 U% f4 H, O8 ?3 Z7 \: X# C# K4 n* N6 j/ w+ h* J. b: F0 w8 Z6 Y4 H4 k* I# N/ p- d& t8 s- }. T0 p4 M: `2 s, Y! Z; W5 D5 X. p/ v; D* T. s+ M3 n8 b2 |* M7 i1 W/ `9 t6 m3 t7 Q2 ]& I6 Y0 ?7 i" P [2 @8 ~* O7 b& p2 _6 h2 K: D v2 L1 O7 _% I6 z8 X* C7 t6 F, s4 c' L. s' A7 C/ E- ^0 E, {9 r( k% g; U' z8 [1 u, k$ ], s# t' J/ J' G |& s1 |. e/ }7 G2 z6 Z) T4 o5 C+ n# r, O7 ^" k9 {: ^5 T2 y4 _( `% U0 f# `9 o) o3 g9 _" M5 k. s6 M8 B7 S T ^; H6 C: }% j% n* a1 [7 s1 Y* M/ O3 @6 M! E l c7 u# `1 V( }6 [; D' L, U! k+ H% L! ~. O0 W* r! M. t# t, e( ~+ \% b5 Z& w. Z+ G( i/ h& ?6 s1 O9 L2 m9 |$ M z# p# x0 B# K' e" W! n$ D4 n& Q: `% N& r" b5 M/ w! _9 O+ k' y2 h# s8 B9 v! m3 p' B1 C. F e2 c2 ?& S" h2 j1 w3 E! t4 F6 t( b" ^" A4 |' f7 i. V9 y4 e9 U; H- E# @5 H# P/ _' o+ R% h- D* K x1 n4 Q. ^8 |. J, \* O, F' S/ z+ Q2 H( C5 _" T7 W/ b( J! d/ }. h7 q/ E; ~, t3 A7 M6 H0 e. S, ^% p# R2 `) \0 u: R0 K7 M& Y- N* f4 x3 `2 J0 p1 ~/ V% X* ?) g) b& f F$ W" ?# D! m( s ~' G- d, |* D6 I: _5 [) I# k! Y8 }, [/ U0 z" m- O v+ R3 U3 B: D0 K ]3 T0 G: P( Y3 K- b: x! _) L2 {* w3 A( f, ?- I/ C+ D/ `% K# X6 h' g
表1 CxNy涂层薄膜显微硬度测试值表
试样号 |
硬度 (GPa) |
平均硬度 (GPa) |
试样号 |
硬度 (GPa) |
平均硬度 (GPa) |
1 |
49.43 |
41.20 |
4 |
42.12 |
40.94 |
36.36 |
39.48 |
37.85 |
41.21 |
2 |
34.88 |
45.18 |
5 |
46.08 |
40.01 |
43.06 |
43.06 |
54.50 |
32.25 |
44.04 |
38.66 |
49.43 |
/ |
3 |
40.33 |
39.77 |
6 |
82.56 |
72.04 |
38.65 |
51.88 |
40.33 |
71.19 | ! x' n0 s/ S, Z; H+ G! X2 G
由表1可见,CxNy薄膜的硬度约在40~72GPa之间。武汉大学物理系在单晶硅基体上沉积了CxNy,其硬度亦达到50GPa。还用划痕法测量了CxNy薄膜涂层的附着力,按JB/T8365-96标准规定,也达到了标准。
, N- V( C0 D* Y' ^8 k6 b% a. L! |2 CxNy表面涂层麻花钻的钻削试验6 V+ Z8 }) N9 q& m, Z/ o4 g z, Y
: F1 e& ~! K% S% ]8 H
- 第一组: : ~' o/ [$ u& k1 t
- 直径为Ø6mm的W6Mo5Cr4V2普通高速钢麻花钻,由武汉大学物理系进行CxNy涂层,涂层薄膜厚度约为4µm。用涂层钻头和未涂层钻头在高强度钢38CrNi3MoVA(经调质,硬度为36~40HRC)上钻孔,孔深约10mm。切削一定时间后,分别测量钻头左、右二刃的后刀面磨损量VB,测量部位为钻头最大直径处的主切削刃后刀面。 e6 N: X! \9 p. P# c* T3 O
- 切削用量:进给量f=0.13mm/r,转速n=530r/min,切削速度v≈10m/min;干切;每钻一个孔,约用10秒。 8 C. s( V! ~% [4 i, B+ e
- 钻头左、右二刃的后刀面磨损量均测量、记录,画成刀具磨损曲线,列于图2。因钻头两个顶面(即主后刀面)刃磨比较对称,故左、右后刀面磨损量很接近。图2中分别画出左、右切削刃的磨损曲线。在图2的横坐标上同时标明了钻孔数和切削时间。
: F. h9 O. r* {3 E- u0 t0 p, C; p( z" a! d$ _2 e9 e: m/ ?$ P, Z* ?, W# f4 D- Z6 n [& @0 O( |& y/ N$ F2 w. O X/ O# W, H- a3 D( K9 a* B
 图1 涂CxNy薄膜的麻花钻 |
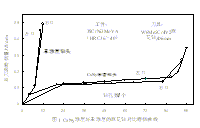 图2 CxNy涂层与未涂层的麻花钻对比磨损曲线 |
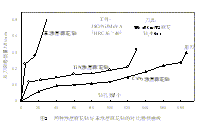 图3 两种涂层麻花钻与未涂层的麻花钻对比磨损曲线 | 5 Y" ^, Z- Y, ~4 Y
- 由图1可见在后刀面磨损量相同情况下,CxNy涂层钻头的切削时间约为未涂层钻头的10倍,故涂层后钻头耐磨性的提高十分显著。
# e A0 `5 b) r7 i2 }/ N5 o2 P
- 第二组:
3 d+ }: Z I6 y3 z0 B G
- 再用直径为Ø6mm的W6Mo5Cr4V2普通高速钢麻花钻,进行CxNy涂层和TiN涂层,在高强度钢38CrNi3MoVA(HRC 36~40)上钻孔,孔深约为10mm。
6 u6 c; N0 `( M$ M) p. o
- 切削用量:进给量f=0.13mm/r,转速n=530r/min,切削速度v≈10m/min;干切;其余切削条件与前相同。每钻一个孔,约用8秒。 ; X$ z: v* l2 p' P# |3 e: O
- 图3为三种钻头的主后刀面磨损曲线,未分左、右切削刃。
* Z$ j% W8 J& B: u
- 由图3可见,在后刀面磨损量相同情况下,CxNy涂层钻头的切削时间约为未涂层钻头的10倍,TiN涂层钻头约为未涂层钻头的7倍,故CxNy涂层的耐磨性高于TiN涂层。
. Y l3 c7 F0 W* Z. H# {, p
3 CxNy复合表面涂层硬质合金刀片的车削试验
, g. P R- I* }* e9 @/ M) L
' s* b( e+ |* @9 a- 第一组: 5 ?3 x: E4 I1 \4 t& t2 @- Y
- 刀具:CxNy复合涂层刀片(YG8基体),未涂层的YG8刀片,国产立方氮化硼(PCBN)刀片; " c: |6 j6 L( I3 [- _6 Z6 c
- 工件:T12A工具钢,淬硬61HRC;
6 W" g' W' z# z& k( |1 s' Y
- 刀具几何参数:前角g0=0°;后角a0=8°;主偏角kr=90°;刃倾角ls=-4°;刀夹圆弧半径re=0.8mm; , r' ~* h& u2 `+ F- a" f }
- 切削用量:切削深度ap=0.5mm;进给量f=0.1mm/r;切削速度v=60m/min;三种刀具的磨损曲线如图4所示。
: l- t8 J+ j+ @7 Z" c+ N3 I# N8 Y - 第二组: % Q- @" T# e+ ~
- 刀具:CxNy复合涂层刀片(YT14基体),未涂层的YT14刀片,国产YBo2涂层硬质合金刀片(TiN涂层); 3 g' k1 v1 C5 K7 b0 N- H6 N
- 工件:60Si2Mn高强度钢,调质,40HRC;
0 B- R3 S1 }, Q" Z n5 R
- 刀具几何参数:前角go=4°;后角ao=8°;主偏角kr=45°;刃倾角ls=-4°;刀夹圆弧半径re=0.8mm; + }% [. l! T& a" G3 L, }8 _6 _' c
- 切削用量:切削深度ap=1mm;进给量f=0.15mm/r;切削速度v=150m/min; 7 v, ^; C6 ?( i
- 三种刀具的磨损曲线如图5所示。
3 z0 {% l' U7 ]) l3 ^0 Z% {4 G( _5 b* j6 p* P5 |1 E% h5 s/ D! _+ s% v5 ?8 k- p( v# V2 F% t& x; ^9 V! @% Z) X3 |0 h' t; s( X% |- T
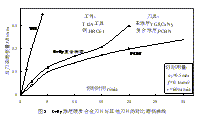 图4 CxNy涂层硬质合金刀片与其他刀片的对比磨损曲线 |
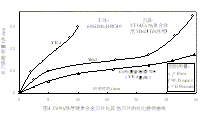 图5 CxNy涂层硬质合金刀片与其他硬质合金刀片的对比磨损曲线 |
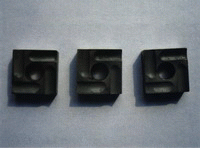 图6 涂CxNy薄膜的YT14硬质合金刀片 |
& Q, _' ^( N! ^8 m) g - 从图4、图5可以看出,YG8和YT14两类硬质合金刀片经涂覆CxNy薄膜后,刀具寿命大为提高。但在车削淬硬钢T12A时,CxNy涂层刀片的使用寿命低于PCBN刀片。在车削高强度中硬钢602Mn时,CxNy涂层刀片的使用寿命略高于YBo2(TiC涂层)刀片。
% W0 Z( M* p' H6 A! {; o0 Q4 分析与讨论
2 I( w, i" Y, W
* J1 q" x9 P" T2 Z- 在高速钢钻头上进行CxNy表面涂层,其使用寿命大大提高;CxNy涂层钻头的寿命也显著高于TiN涂层钻头。在高速钢刀具上涂覆CxNy,其涂层技术已日趋成熟,使用效果亦日趋稳定。 . N% l2 V' m- t( e# |: _
- 对于硬质合金刀片,经过CxNy涂层,刀具寿命也能提高,但提高幅度不如高速钢刀具那样大。在车削淬硬钢时,其刀具寿命尚低于PCBN刀具;在车削高强度中硬钢时,其刀具寿命仅略高于TiN涂层硬质合金刀具,这样就限制了CxNy涂层硬质合金刀具的应用。
0 v6 X: P7 d# j; f) s
- CxNy涂层材料的各项力学、物理性能,需作全面的测试和深入研究。CxNy涂层和硬质合金基体材料之间的匹配也有待认真研究。 9 i1 a$ j# [- P( a# `5 I
- CxNy涂层属超硬材料,它与铁族元素呈惰性,故这种刀具可以加工钢铁材料。这是一个很大的优点,可以补充金刚石刀具的不足,从而有着广阔的应用领域。预计经过认真的研究和探讨,CxNy涂层超硬刀具有着美好的发展前景。
$ b1 K/ `( _, s0 i6 C. h. E# e; O
|
|