|
马上注册,结交更多好友,享用更多功能,让你轻松玩转磨削论坛
您需要 登录 才可以下载或查看,没有账号?注册会员
×
刀具基体表面粗糙度直接影响金刚石薄膜与基体的实际接触面积和接触状态,是影响金刚石薄膜涂层刀具附着强度的重要因素。本文从金刚石薄膜在基体表面的成核密度、成核状态及机械锁合作用等方面研究了基体表面粗糙度对金刚石薄膜涂层刀具附着强度的影响。
4 K+ z0 s u6 v1 基体表面粗糙度对成核密度及成核状态的影响
, J- Q' g0 E$ A5 F k: W* T9 j7 s" X0 M. R: P8 ]3 M
) z* R8 q/ s7 K; N$ j3 A& D) n( Z6 A2 Z: `9 D8 J4 X: w, c. O; c: x
+ o( S* ]8 z4 {; Z/ U% }
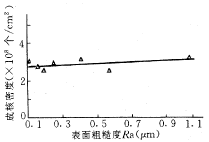 图1 基体表面粗糙度对成核密度的影响
| 0 d6 V, _, T0 T+ T2 Q* `
为研究刀具基体表面粗糙度对成核密度的影响,我们以用不同粒度金刚石微粉研磨过的基体为试样,进行了实验研究。为避免WC-Co系硬质合金中Co元素对成核的影响,我们以金属W为基体用燃焰法进行了沉积实验。实验条件为:反应气体流量比O2/C2H2=1,基体温度约750℃,沉积时间为3min。根据扫描式电子显微镜观察计算结果,基体表面粗糙度与金刚石薄膜成核密度的关系如图1所示。
4 ^; a& o' q& a. `$ g& t
' x7 S# e) l; f6 f& }7 F从图中可以看出,以W为基体时,基体表面粗糙度对金刚石薄膜的成核密度没有太大影响,在上述沉积条件下,成核密度可达 3×108个/cm3左右。对WC-6%Co硬质合金的研究也表明了同样的趋势。这与在单晶Si片上的沉积实验结果不同。可以认为W和WC-6%Co硬质合金中存在的大量晶界缺陷促进了金刚石薄膜的成核,从而使由基体表面粗糙度差异带来的对成核密度的影响变得不十分明显。
! h0 \5 ?4 A! M% ]/ D 9 F) g: C3 h! p. v0 S- o. p
! r. O; D+ o. Q H8 c/ J! S: M8 U# \: y5 L4 r7 c( L4 M9 m; a4 W4 H* m% i" O. y# z4 V/ W3 L( M, B" C1 c1 D6 G# G3 g' e+ P# p, }5 R& o5 c$ K4 ?
3 x- P5 N; V8 W8 w1 b 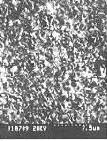 (a)Ra0.19µm
|
* _. z% M& X. k' s5 x 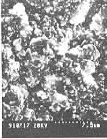 (b)Ra0.41µm
|
% k7 g$ M& f& U! L2 t j0 c4 { 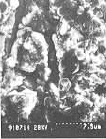 (c)Ra1.04µm
|
图2在不同粗糙度基体表面上金刚石的成核状态 | # e3 ]/ N9 F8 l9 v9 ^3 n
用扫描式电子显微镜进行进一步的观察分析表明,基体表面粗糙度对金刚石薄膜的成核状态有较大影响。图2为在具有不同粗糙度的基体表面沉积2min未形成连续薄膜时金刚石的成核反晶粒生长状态。从图中可以看出,在 Ra0.19µm的较光滑基体表面,金刚石薄膜较平整,金刚石薄膜与基体的接触局限于成核点附近,可近似认为是二维接触,实际接触面积较小。在Ra0.41µm和Ra1.04µm的粗糙基体表面,金刚石在凸峰及凹谷中均有成核,由于金刚石晶粒呈三维生长,所以在形成连续薄膜后,在凹谷中成核的金刚石晶粒与基体呈三维接触,使金刚石薄膜底面与基体的实际接触面积显著增大,从而有助于提高金刚石薄膜与基体间的附着强度。但在Ra1.04µm时,由于基体表面太粗糙,凸峰间的凹谷较深大,在金刚石晶粒进一步生长形成连续薄膜后容易在凹谷中形成空穴。
8 B1 W% s1 c9 I# f% D2 刀具基体表面粗糙度对附着强度的影响, z8 |$ }# z: L0 I
为进一步研究刀具基体表面粗糙度对附着强度的影响,我们用燃焰法制备了具有不同基体表面粗糙度的金刚石薄膜涂层刀具。由于WC-Co系硬质合金中粘结相Co在沉积初期有促进石墨形成的作用,为排除其影响,实验中选择了金属W为金刚石薄膜涂层刀具的基体材料。
3 y3 i9 v. [/ b, _; Z5 z* R
7 E2 a G. O" R2 G4 h由于金刚石与基体附着强度的定量测定较为困难,目前应用最多的是压痕观察法,即用洛氏硬度计以一定压力将压头压入金刚石薄膜,根据薄膜剥落面积的大小定性对比附着强度的大小。考虑到金刚石薄膜涂层刀具实际应用的特点,我们采用了断续车削工件的方法来评价其附着强度的大小。即在一定切削条件下,用金刚石薄膜涂层刀具进行断续车削实验,以金刚石薄膜剥落时的耐冲击次数和薄膜剥落面积大小来评价不同金刚石薄膜涂层刀具的附着强度。断续车削实验条件如附表所示。 % K! @& j- t2 O
7 C( P! @, \) a; r* M, s: D; M
+ a# ^: t8 Q2 _( V# }/ I+ l7 K( u8 J0 `2 Q! k+ x2 R$ h# m& x% a! W3 t4 x! y v2 {' T) H) E8 D( g' i% l) X K' F1 F+ _* A4 j6 H v3 S9 s+ h& {0 v" S. D! s" ?' c W
! Q( c4 N7 R! _$ }4 Q5 e( J4 |. `' N1 ]+ C \) L; s: T* @" I8 B1 N# Y* R3 K3 c4 j9 E n( ] e9 w: a, I& ~2 S1 { f. n) Q2 J2 {% j, {+ Q" t2 |' S& ]( G; Q, q4 E; r( S, F( i* X5 s; f5 ]. o0 P+ L5 n. u+ P2 `; G: w$ S. @* Q' G }" n0 c% ]' b( E2 V! i7 c1 y4 T8 U7 N7 o. i+ W# t2 U* x) f8 K! L4 d; v. C- J8 f+ G4 ?9 b: [8 m6 B q% I8 C2 h( g& L
金刚石薄膜涂层刀具断续车削实验条件
工件材利 |
工件截面形状 |
刀具角度(°) |
切削用量 |
冷却润滑 |
LY12 |
" ?4 k' }) r" Q* Q! w 
|
g0=-5° a0=5° Kr=Kr’=45° |
v=130m/min ap=0.5mm f=0.1mm/r |
干式切削 | |
$ O, f3 ]+ q- M6 D; v. x. _4 ?5 U 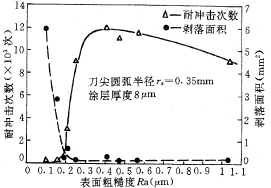 图3 基体表面粗糙度对附着强度的影响
|
$ m+ j! P, w, f9 ?" q# A 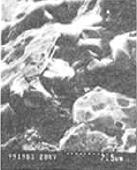 图4 由于机械锁合作用残留在基体表面的金刚石晶粒
| 2 J3 G/ W: C% J2 n& k
在附表中所示切削实验条件下对LY12进行断续车削实验,基体表面粗糙度与金刚石薄膜涂层刀具耐冲击次数和薄膜剥落面积的关系如图3所示。从图中可以看出,随着刀具基体表面粗糙度值的增大,薄膜剥落时金刚石薄膜涂层刀具的耐冲击次数显著增加,薄膜剥落面积大幅度减小,说明金刚石薄膜与刀具基体间的附着强度随基体表面粗糙度值的增大而显著提高,完全可满足实际切削加工的要求。从图中还可看出当基体表面太粗糙时,附着强度有下降趋势。
( N$ o. S& ]: n2 U. h7 X' h
9 |) r( f+ l' c1 r用扫描式电子显微镜对金刚石薄膜剥落后的基体表面进行观察分析,结果表明:在较光滑的基体表面几乎没有金刚石晶粒的残留;在粗糙表面的沟槽和孔洞中残留着许多金刚石晶粒如图4所示。可以认为,在粗糙的基体表面,不仅金刚石薄膜与基体接触面积较大,而且在粗糙表面沟槽和孔洞中嵌合的金刚石晶粒使金刚石薄膜与基体之间建立了机械锁合作用,从而使附着强度得到了显著提高。当基体表面太粗糙时,由于在金刚石薄膜与基体之间容易形成空穴而使附着强度下降。 - H) _' L( D0 A4 X9 }7 ^" k
3 结论" j9 u$ l5 N! r Z- z+ J& ^
在W和WC-Co系硬质合金基体上沉积金刚石薄膜时,基体表面粗糙度对成核密度没有太大影响,但对薄膜和基体间的接触状态有较大影响。较粗糙的刀具基体表面不仅使金刚石薄膜与基体实际接触面积增大,而且可在金刚石薄膜与基体之间建立具有宏观效应的机械锁合作用,从而使金刚石薄膜涂层刀具的附着强度得到显著提高。当基体表面太粗糙时,在基体表面和金刚石薄膜之间将由于空穴的存在而使附着强度下降。合理设计刀具基体表面粗糙度是提高金刚石薄膜涂层刀具附着强度的有效手段。
" I4 [7 R! P& U- j* n8 G5 ] |
|