马上注册,结交更多好友,享用更多功能,让你轻松玩转磨削论坛
您需要 登录 才可以下载或查看,没有账号?注册会员
×
双频淬火装置如图1,其包含两只并排的感应器分别供给不相同频率的电流。上感应器通入较低的频率,工件移动使加热深度较深(低频率);而下感应器通入较高的频率,工件移动使加热深度较浅,此深度相当于所需的硬化层厚度。 4 y# q+ D+ \. V9 @
1 工件; 2,3 频率分别为f1和f2的感应器; 4,5 磁芯(导磁体) 图1 双频淬火装置简图 选择两只感应器的功率使上感应器加热工件到居里温度,下感应器在相同时间内沿着顺磁性的工件加热到淬火温度。要设计双频淬火装置的各种参数,有必要作系统的电磁计算,但在专门的文献中缺乏适当的计算方法介绍[1]。
1 轧辊双频感应淬火的数学分析
1.1 简化的假设和计算模型
求解双频感应淬火过程的电磁问题是一个复杂的数学问题,困难在于系统零件的有限尺寸、工件电磁参数的非线性变化以及感应器移动速度对特征现象的影响。充分考虑所有的这些因素,则解法复杂,以致于无法实用。于是在对解答的精确性影响不大的前提下,引入三类简化的假设:
(1)有关工件-感应器系统的几何形状假设:
a.以无限长的轧辊代替有限长度的加热工件; b.以有限高度和微小厚度的环代替有限尺寸感应器; c.一个无限长的圆柱体代替两个有限尺寸感应器的磁芯。
(2)有关工件电磁参数的假设:
a.淬火加热过程可以分成两个阶段。第一阶段,铁磁性工件仅仅由频率f1的感应器在一定厚度内加热到居里温度(这厚度近似等于穿透深度即趋肤深度);第二阶段,频率为f2的感应器加热的工件可分两层,外层是顺磁性材料(μr=1),而内层是仍保持高导磁率的铁磁性材料,参数μ和σ在每一层的体积内作为一常数。 b.两层中导磁率可由众所周知的方法[2]为基础计算得到,为简化起见内层的导磁率均作为无穷大; c.把频率f1感应器加热得的表面铁磁性层厚度与频率f2感应器加热得的表面顺磁性层厚度看作相等。
(3)为了避免积分方程式的问题而假设:
a.不计感应器的移动速度; b.把工件沿着坐标线Z=0分开,这样把每半只轧辊均看成无限长,照图2的两种情况分别计算,然后将得到的介于适当的区内结果进行合并。
图2为考虑所有这些假设的计算模型。
5 q5 Q \1 C9 L' d) ^6 A$ B$ y 图2 工件“分开”后的计算模型 1.2 矢热微分方程式的通解
从麦克斯韦尔(Maxwell)方程式计算推出矢势的微分方程式,在圆柱体坐标中有下列形式[3、4]: , n( d: c! i6 z) W3 T
 式中: m2=jωμσ; ω=2πf电流脉动数(即角频率);μ——介质的导磁率;σ——介质的电导率
电磁场矢量可用A以下列形式表示: . T; ?, M) `! M8 t( q0 ^/ w
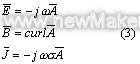 式中: E——电动势; B——磁感应强度; J——涡流密度
方程式(1)的特解可由分离变量法求出,为
A(r,z)=[C(k)I1(pr)+D(k)K1(pr)]]×[F(k)coskz+G(k)sinkz] (4)
式中:C(k),D(k),F(k),G(k)——积分常数 I1,K1,I0,K0——修正的贝塞尔(Bessel)函数 k——分离变量常数
p=(k2+m2)1/2 (5)
方程式(1)的通解是(4)式的所有特解形式的总和,于是: . \+ s% D1 G( N! n+ ^) j1 ~
 在图2的特殊计算区间中,(6)式的解有多种形式。事实上从应用的观点出发,最本质的是工件的外层(区域Ⅱ),仅仅这个区域解的结果如下:
- L [+ S, E2 K+ a, k5 y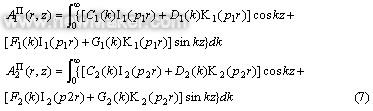 式中:p1=k2+jω1μ21σ21
p2=k2+jω2μ22σ22
符号Ⅱ表示计算的Ⅱ区域,而记号1和2分别表示频率f1[图2(a)的情况]和f2[图2(b)的情况]感应器的有关量。
表达式(7)中出现的积分常数可用矢势并符合图2的边界条件求出,有
) ^6 o2 B3 m! u( X# X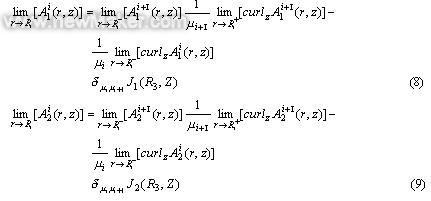 式中:μi——在i区域中的导磁率
式中:I1,I2——频率f1和f2的感应电流; n1,n2——频率f1和f2的感应器匝数 H,h——感应器1、2分别对应的工件长度(见图2)
基于边界条件(9)算出积分常数,于是求得工件的矢势。
) v8 M. x2 \1 I" D3 n1 e& b$ v, a# H6 b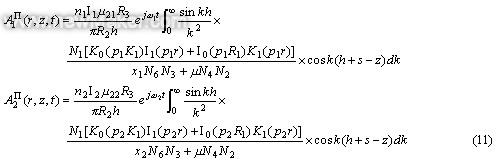 式中:N1=K1(kR3)I0(kR4)+I1(kR3)K0(kR4) N2=K0(kR2)I0(kR4)-I0(kR2)K0(kR4) N3=K1(kR2)I0(kR4)+I1(kR2)K0(kR4) N4=I1(p1R2)K0(p1R1)+K1(p1R2)I0(p1R1) N6=I0(p1R1)K0(p1R2)-K0(p1R1)I0(p1R2) M4=I1(p2R2)K0(p2R1)+K1(p2R2)I0(p2R1) M6=I0(p2R2)K0(p2R1)-K0(p2R2)I0(p2R1)
x1=p1/k;x2=p2/k (12)
μr1,μr2——在图2(a)和(b)情况中的相对导磁率
1.3 工件中磁感应强度、涡流密度和有效功率密度
区域Ⅱ中与(3)式相一致的磁感应强度有二个分量BrII和BzII,按式(11)可得下式:
; i, h T+ P0 j8 |3 m) G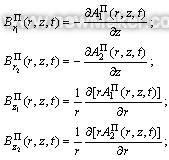 由于矢势(11)式的微分无实际意义,这也就没有给出磁感应强度的表达公式,但轧辊表面(r=R2)的磁感应强度分量(Bz)通过(13)式借助于计算机算出,结果示于图3中。
% ?! Z) B# B/ n, L4 f6 \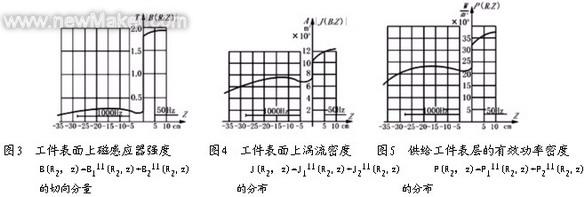 工件上的涡流密度按(3)式可得:
0 Y1 e' M) ]) ?( q" ~ 轧辊表面(r=R2)的涡流密度按上式计算,结果示于图4中。
工件表面的有效功率密度可按下式计算: 7 ^$ i. w* h) O; E& ~" G) ^; t) C9 y
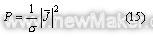 由(14)得:
! _* s* b& u4 W) R9 k4 D 按式(16)计算的有效功率密度示于图5中。
2 轧辊双频淬火试验
根据上述计算,上感应器选用50 Hz,下感应器保持1000 Hz频率。轧辊双频淬火试验的同时,对轧辊的温度分布进行了测量,结果见图6.
+ }# a' _' e7 J! D& S# S8 J# R+ B 1,2,3,4,5,6离表面不同的距离的温度分布 图6a 双频感应淬火时的温度分布 % y+ M6 N1 c) A+ @* J" c( |* ~
(离轧辊表面的距离) A淬火加热始瞬间温度;B通过50 Hz感应器后的温度; C通过1000 Hz感应器后的温度;D喷雾的瞬间温度 图6b 轧辊的截面Ⅰ的温度分布 由图6a可知,淬火过程的温度的分布有三个最高点,第一个最高点(t=3 min)相应于预热后的温度,第二个最高点(t=21 min)相应于通过50 Hz感应器后的温度,第三个最高点(t=25 min)相应于通过1000 Hz感应器后的温度。图还表明,适当的淬火温度开始于工件温度250 ℃后的第16分钟,精确来说大约加热仅10分钟,第27分钟后喷雾,处理即结束。淬火中轧辊的温升平均速度大约是1.2 ℃/sec,辊身截面的温度分布见图6b.与单频淬火得的温度分布相比,可以看出:轧辊表面在深度30 mm内的温度差,后者约210 ℃,而前者仅120 ℃,从而保证得到更厚的硬化层和较小的硬度梯度(图7). ( P) C7 b7 L' _6 r* M
(离轧辊表面的距离) 1一次预热的单频感应淬火; 2一次预热的双频感应淬火 图7 轧辊的截面硬度分布 3 结 论
1.双频感应淬火的上述计算方法具有较强的通用性和实用性。 2.双频淬火较单频淬火能使工件获得更好的性能(表面硬度,截面硬度梯度、硬化深度),并提高工效和降低能耗。
( |* P! H k: v) D |